Presentations
Tuesday, November 24th
KEYNOTE: Unlocking treatment options in today´s spine tumor care, by
Roger Stadler, CEO icotec ag
icotec ag is world market leader in the treatment of spinal tumors with BlackArmor® (Carbon/PEEK) implants and provides intensive support to radiooncologists and surgeons in the further development of comprehensive tumor therapy from planning to implementation and follow-up.
_____________________
Seamless solution for industrial-grade continuous carbon fibre 3D-printed composites, by Tanja Koch, Product Growth Specialist at 9T Labs
Nowadays, the comparably high costs associated with carbon fiber (CF) composite parts to its aluminium or steel contenders remain a constraining factor. A higher degree of freedom to optimize the part geometry and the fiber layup in combination with increased automation in manufacturing will reduce the current constraint. 3D printing, an additive manufacturing technology, is believed to deliver on those demands for manufacturing. 9T Labs’ radical all-in-one Red Series technology provides a fully integrated solution, starting from CAD design to final part. Further, it enables 3D printing of performance composites with high fiber volume content (>60%) materials, ensures part quality by introducing appropriate consolidations steps, and scales through parallelization of affordable printing units.
______________________
MOWA – a next generation modular orthosis system, by
Gion A. Barandun, Professor at the OST Eastern Switzerland University of Applied Sciences
The configuration and adaption of orthosis is difficult, as the individual patients‘ needs are hard to capture. Additionally, the manufacture and tuning of the structural composite elements and parts in direct contact with the patient are time consuming and prone to errors. The MOWA system offers a new approach, based on modular components adapted to the patient using a new process. By „measuring“ the patient and then selecting and producing the appropriate components of the orthosis, an optimal patient care is ensured.
______________________
Unidirectional continuous fiber-reinforced thermoplastic semi-finished products and their advantages in technical and medical applications, by
Sebastian Iwan, Managing Director of thermoPro ENGINEERING GmbH
The present paper introduces the fully impregnated semi-finished product thermoPre®. The material development is characterized by using a single, direct processing technique in a large-scale manufacturing process. Apart from the actual material production, the lecture will present the main features of component development. From material characterization to component and tool design to component testing and prototype production.
_______________________
SkolioShirt - Development of an innovative scoliosis corset including a new manufacturing process, by
Lena Kölsch, research assistant at Fibre- & Materials Development, Faserinstitut Bremen e.V. (FIBRE)
Scoliosis is a deformity of the spine that develops during growth of children. The spinal column bends sideways and the vertebral bodies twist at the same time. The disease is associated with degenerative changes and increasing limitation of physical performance. In the case of moderate to severe scoliosis, treatment with a scoliosis corset is part of the therapy. The main disadvantage of this therapy is the lack of acceptance due to the wearing comfort and the visibility of the corset on top of the clothes. The success of the therapy depends strongly on the amount of time in which the corset is worn.
Therefore, the aim of the project is the development of an innovative corset made of fibre reinforced composites, including a new manufacturing process. The innovative scoliosis shirt should lead to a higher therapeutic success compared to previously available solutions due to the improved wearing comfort.
The design concept is based on a combination of a CFRP (carbon fibre reinforced plastics) inlay produced by a vacuum infusion process and a textile cover. The inlay applies and transfers the forces, especially in the pressure zones, and the textile cover gives the corset the appearance of a garment and ensures a better wearing comfort. An innovative construction of the inlay, in which textile patches are layered, allows the stiffness and strength of the material to be varied locally and thus adapted to the individual requirements of the patients. The use of CFRP and the special design that is adapted to local loads can reduce the amount of material used and thus also the weight. Furthermore this results in an improved wearing comfort. In addition, FEM simulations of a corset, which is available on the market, were used to analyze the mechanical stress and to develop the inlay.
______________________________________________________________________
Wednesday, November 25th
KEYNOTE: Composites in medical technology. From the beginnings to today and a look ahead to the future, by
Axel Herrmann, CEO CTC GmbH und Head of Fibre-Institut, Bremen
In this keynote we will look at the development of composite materials in medical technology applications, using examples as well as looking at the characteristics of composite materials for use in medical technology.
______________________
The Application of Reverse Engineering & Additive Manufacturing Technologies in Neurosurgery, by
Sven Duda, Chief Medical Officer at Clinic for Neurosurgery Westerstede Military Hospital, and
Marc Mayer, M.Sc. at CTC GmbH & Laboratory for Manufacturing Technology Helmut Schmidt University
Today, surgical planning is supported by various sectional-imaging techniques. As the image information does mainly depict two-dimensional image stacks in different layers, the transfer of the two-dimensional image data to the surgical site is to be made by the surgeon with the help of his personal experience and spatial imagination. With the application of image segmentation and 3D printing the sectional images can be transformed to 3D models to be used for surgical planning and simulation. The fabrication and testing of a novel simulator for teaching of basic surgical skills for the management of head trauma are presented. Furthermore, a way forward for the gradual development of even more realistic surgical simulators is shown.
_______________________
Development and use of thermoformable composites in orthopedic applications, by
Markus Brzeski, Managing Director of A+ Composites GmbH
Composites are an elementary component for the reinforcement of orthopedic aids. This presentation will show how orthopedic technicians work together with composites specialists and how they develop new products.
________________________
When haute couture fashion meets biomimetic design: How to improve medical imaging, by
Benedikt Borchert, Sales Manager at Biontec - Bionic Composite Technologies AG
With increasing efforts to reduce the impact and side effects of any medical treatment, imaging technology becomes more and more important. Engineers seek to increase doctor’s field of view while reducing patient’s radiation exposure. With innovative radiolucent components, Biontec helps to achieve this goal.
_________________________
Tailoring the implant stiffness by hybrid composite material design, by
Yves Becker, R&D Engineer, Component Development, Institut für Verbundwerkstoffe GmbH
In recent years, carbon fiber reinforced polyether ether ketone (CF-PEEK) is increasingly used for implant applications. In contrast to metallic implant materials, it offers a unique combination of properties such as biocompatibility, radiolucency, low density and excellent structural mechanical properties. In this study, a hybrid thermoplastic composite pedicle screw is focused. This screw shows a unique combination of a reinforcing CF-PEEK element in its center and short CF-PEEK material for its outer shape.
Ensuring sufficient interface strength between the components, the implant stiffness can be tailored and the problem of stress shielding can be reduced by this approach.
______________________________________________________________________
Thursday, November 26th
1-to-1 Matchmaking Sessions
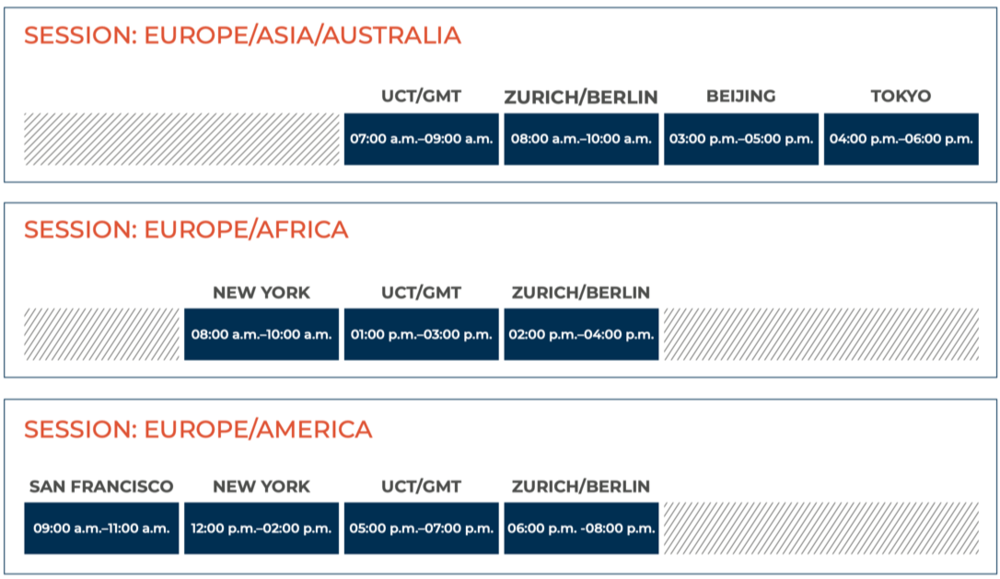